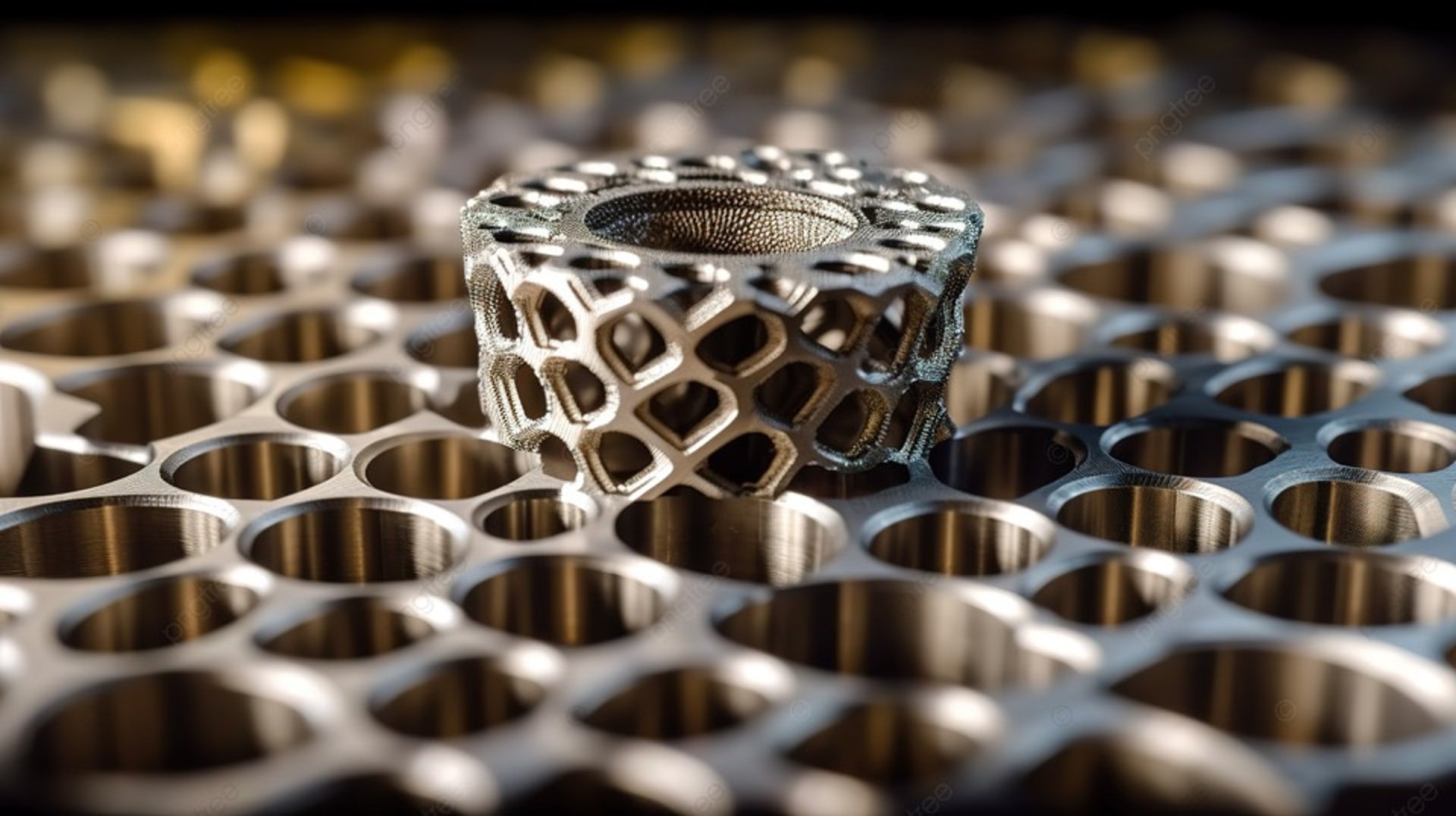
What is Metal 3D Printer?
A Metal 3D Printer is a type of additive manufacturing system that specializes in creating three-dimensional objects using metal materials. Unlike traditional manufacturing methods, which often involve cutting away material to create a shape (subtractive manufacturing), metal 3D printers build objects layer by layer directly from a digital 3D model. This process allows for the creation of complex geometries and designs that would be difficult or impossible to achieve with traditional manufacturing methods.
The technology behind metal 3D printers has evolved significantly since the early days of 3D printing, which mainly focused on plastic materials. Today's metal 3D printers can use a variety of metal materials, including steel, titanium, and aluminum, making them suitable for a wide range of applications, from aerospace and automotive parts to medical implants and custom tools.
The process typically involves the use of a laser or electron beam to selectively melt or fuse metal powder particles, layer by layer, to form a solid object. This method allows for high precision and can produce parts with complex internal structures and fine details.
Metal 3D printing is particularly valued for its ability to rapidly produce prototypes for testing before mass production, as well as its ability to manufacture parts that are lightweight yet strong, often with unique properties that cannot be achieved with traditional manufacturing methods. This makes metal 3D printing a key technology in industries where customization, complex geometries, and the optimization of material usage are crucial.
The Benefits of Metal 3D Printing
Metal 3D Printing offers a range of benefits over traditional manufacturing methods, making it an increasingly popular choice in various industries, including aviation, space, automotive, medical, and research and development. Here are some of the key advantages:
Greater Design Freedom: Metal 3D printing allows for the creation of complex and intricate designs that are often impossible to achieve with conventional manufacturing methods. This includes complex internal structures and geometries.
Lighter Structures with Lattice Designs: The ability to create lattice structures within parts can significantly reduce weight without compromising strength. This is particularly advantageous in industries like aerospace and automotive, where weight reduction is critical.
Single-Step Production of Assembled Parts: Metal 3D printing can produce parts that would traditionally require assembly from multiple pieces. This not only speeds up production but also enhances the strength and integrity of the final product.
Reduced Material Consumption: Additive manufacturing builds objects layer by layer, using only the material that is needed. This contrasts with subtractive methods, where excess material is removed and often wasted.
Reduction of Waste Material: As a result of its efficient use of materials, metal 3D printing significantly reduces waste, which is both cost-effective and environmentally friendly.
Faster Production Possibility Depending on Geometry: Depending on the complexity of the design, metal 3D printing can be faster than traditional methods, especially for small batches or custom items.
Ability to Create Complex Parts in a Single Step: Metal 3D printing excels at producing complex parts that would either be impossible or very costly to create with traditional methods.
Given these advantages, it's anticipated that the use of metal 3D printers will continue to grow, expanding into new areas and applications in the coming years. This technology is not only revolutionizing how products are designed and manufactured but also opening up new possibilities in terms of material properties and the performance of final products.